“On était réputés pour avoir mauvais caractère, mais sur la qualité, c’est sûr, il n’y avait rien a dire !”
Il y avait un savoir-faire remarquable, les gens y tenaient beaucoup. Moi je dis toujours : j’ai une culture de la qualité. On n’avait pas de service contrôle. Et pourtant on n’avait jamais de retours, c’était vraiment exceptionnel. Tout le monde était attaché à faire du bon boulot. Ça c’est clair.
L’usine a fini avec un très très haut niveau technique. On était réputés pour avoir très mauvais caractère et des problèmes de délais, mais tout le monde savait qu’au niveau de la qualité du travail qui sortait de chez nous, il n’y avait pas mieux. Au moment de la fermeture de l’atelier, j’ai vu des courriers de Cartier qui disaient : « non n’arrêtez pas on a besoin de votre qualité« .
Après 68, on a fait dans l’usine un laboratoire de recherche. Il y avait 40 ingénieurs et techniciens à Paris. Ce labo, plus la stabilité du personnel faisaient de notre société une société très pointue du point de vue qualité. Livrer une pièce qui n’était pas parfaite, personne ne faisait ça. Ça repartait tout de suite à la fonderie. Par exemple, on avait un fondeur d’or, il était capable de savoir à 7 degrés près la température de ce qu’il fondait. À l’œil seulement ! Il était extraordinaire et face à ça, les techniciens ils fermaient leur bouche. Il a mis 4 à 6 ans pour apprendre ça.
Il y avait un vrai savoir-faire intéressant et les gens en étaient très fiers.
Pour tout ce qui était chaudronnerie platine par exemple et fabrication de fonte filière, on était les meilleurs du monde. C’est pour ça d’ailleurs que les Allemands étaient contents de récupérer deux employés de chez nous, dont un qui doit encore y être d’ailleurs, je crois qu’il est responsable de l’atelier chez eux parce qu’il a un savoir-faire…
Ces gars-là, c’étaient des artistes faut le reconnaitre. D’autant plus qu’ils avaient dans leurs mains quelque chose qui a de la valeur.
Quand ils faisaient un bassin d’affinage de verre (moi j’appelle ça une cocote minute) 80 kilos de platine, un grand truc avec des tuyaux qui sortent de partout, on met le verre en fusion à décamper dedans, comme un pot-au-feu. 80 kilos de platine, vous n’avez pas intérêt à rater une soudure. On avait des artistes.
“C’était passionnant, on a invente les outils pour fabriquer les pièces.”
Il y avait des travaux d’une très grande technicité. Ils nous demandaient parfois des trucs qui n’existaient pas, et comme on était outilleurs, il fallait inventer l’outillage. De ce point de vue là, c’était passionnant, on a inventé les outils pour fabriquer les pièces.
Moi j’ai eu une dizaine d’années où j’allais au boulot avec plaisir. Je dois le dire, je n’ai pas honte. Pendant une dizaine d’années, j’ai eu un boulot vraiment très intéressant. Un responsable arrivait et nous disait tiens j’ai vu ça sur une foire, démerde-toi pour trouver et pour sortir les pièces. Il fallait d’abord créer la matière première, repérer ce dont on avait besoin, ensuite créer l’outillage puis mettre ça en production.
Ici la main d’œuvre était ultra stable. Le turn-over était ridicule. Alors qu’en Angleterre le turn-over devait être de 30 ou 40%. C’est des métiers qui s’apprennent sur le tas et parfois il faut 3 ou 4 ans pour être « un bon ». Alors évidemment les grands bijoutiers français ils ne s’intéressaient pas aux Anglais. C’est toujours le même problème avec une rotation très forte, sur des métiers où il n’y a pas de transmission, le savoir-faire se perd. Par exemple, on faisait des tubes avec des alliages de métaux. Les Anglais sont venus quatre fois, ça me mettait en colère, ils ont essayé plusieurs fois de faire la même chose, mais ils n’ont jamais réussi. Il y a un gars qui est allé installer la machine en Angleterre. Mais ils n’ont jamais été capables de l’installer complètement.
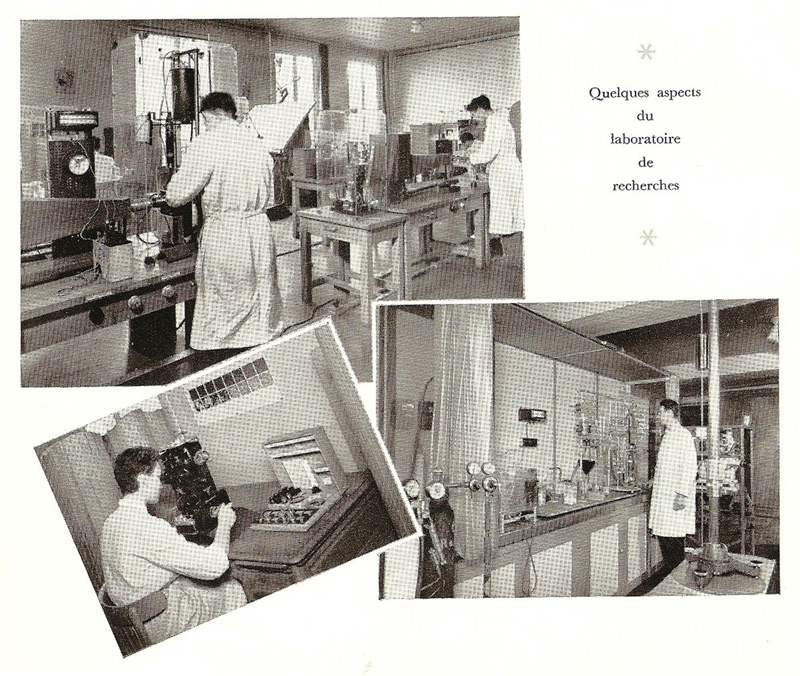
1957
Transmission des savoirs, apprentissage
“Une formation sur le tas qui ne s’apprend pas dans les livres.”
J’ai continué à être formé sur place et j’ai aussi fait des formations. J’ai fait un 1 an de formation en métallurgie, c’était à Paris dans un centre. C’était payé par la boite, c’est eux qui m’ont sollicité pour y aller. De là, j’ai appris pas mal de choses au bout d’un an de formation.
On était nombreux dans mon service. Uniquement dans l’atelier on était à peu près une cinquantaine. Mais dans mon secteur à moi ou je fondais l’or on était à deux ou moi tout seul. Au début il y avait quelqu’un avec moi que j’ai formé et après j’étais tout seul. Parce qu’après j’ai eu beaucoup d’évolution, je suis partie en Écosse pour apprendre à travailler sur une machine. C’était une machine révolutionnaire. J’ai fait à peu près un mois en Écosse pour apprendre à utiliser cette machine qui servait pour les dentaires. Je faisais entre 20 et 60 kilos de dentaire dans cette machine.
On était à deux. Je suis parti là-bas pour me former parce que c’était une machine très compliquée. Et après cette machine on l’a eu chez nous. Il n’y en avait pas beaucoup dans le monde. Ça faisait des tout petits fils et ces fils-là étaient appropriés pour faire des dentaires.
Jusqu’à la fin j’ai fait les lingots aussi. Je travaillais sur les dentaires et je faisais en même temps les lingots. Je formais des gens aussi. On travaillait beaucoup de métaux qui étaient dangereux au niveau de la santé. Moi je les travaillais très très peu, il fallait avoir un masque.
- 1993 CLAL Brochure Savoir faire – Extraits
- 1993 CLAL Brochure Savoir faire – Extraits
- 1993 CLAL Brochure Savoir faire – Extraits
- 1993 CLAL Brochure Savoir faire – Extraits
- 1993 CLAL Brochure Savoir faire – Extraits
- 1993 CLAL Brochure Savoir faire – Extraits
- 1993 CLAL Brochure Savoir faire – Extraits
- 1993 CLAL Brochure Savoir faire – Extraits